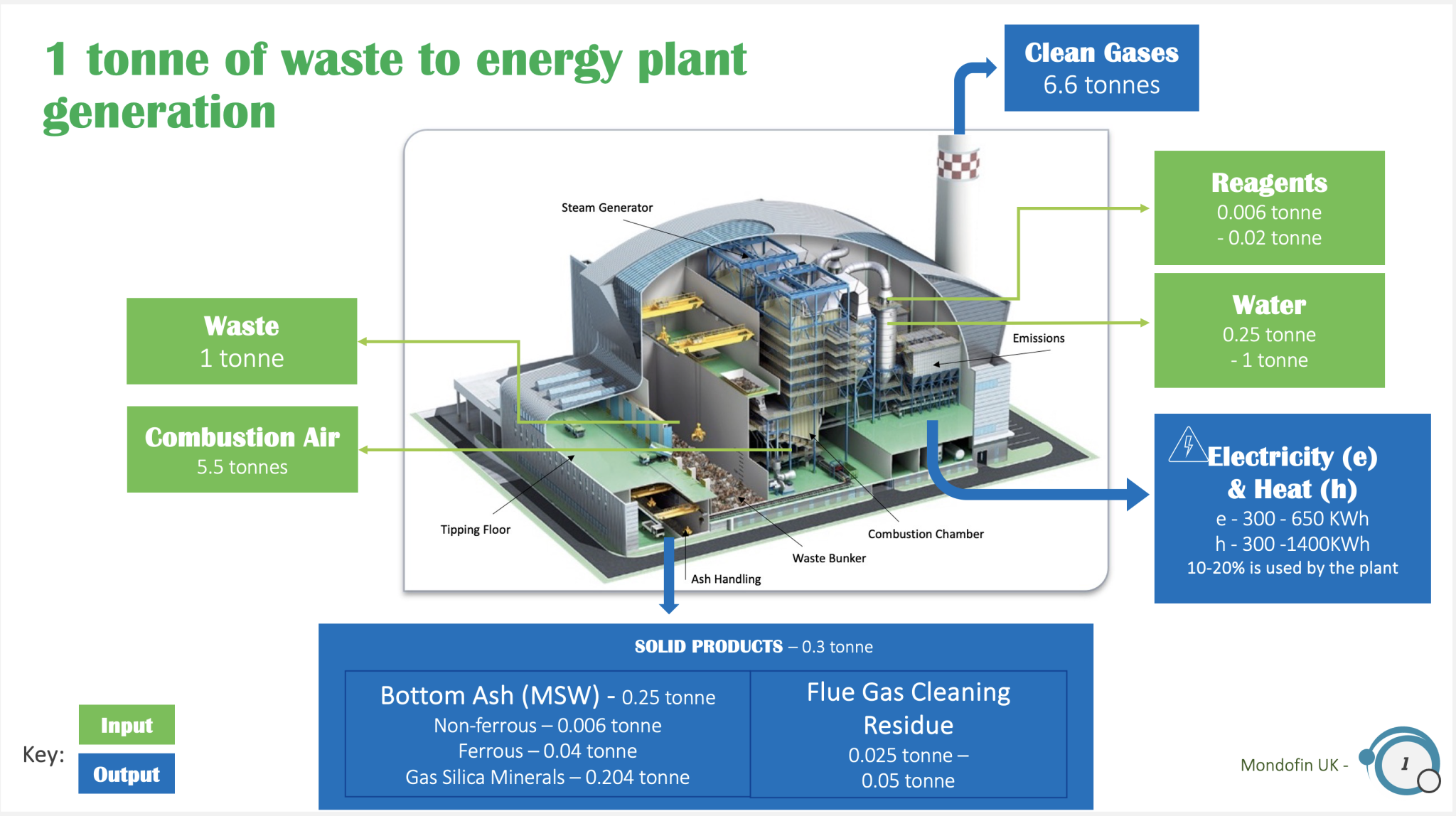
What is Waste-to-Energy (WTE)?
Ecologically Sound, Cost-Effective Energy
Waste to energy (WtE) is a vital part of a strong and sustainable waste management chain. Fully complementary to recycling, it is an economically and ecologically sound way to provide a renewable source for energy while diverting waste from landfills.
A WtE plant converts solid waste into electricity and/or heat – an ecological, cost-effective way of energy recovery.
A waste-to-energy (or energy-from-waste) plant converts municipal and industrial solid waste into electricity and/or heat for industrial processing and for district heating systems – an ecologically sound, cost-effective means of energy recovery. The energy plant works by burning waste at high temperatures and using the heat to make steam. The steam then drives a turbine that creates electricity.
Recover valuable resources
Energy from waste (EfW) isn’t just a trash disposal method. It’s a way to recover valuable resources. Today, it is possible to reuse 90% of the metals contained in the bottom ash. And the remaining clinker can be reused as road material.
The results and benefits are proven:
- Avoids methane emissions from landfills
- Offsets greenhouse gas (GHG) emissions from fossil fuel electrical production
- Recovers/recycles valuable resources, such as metals
- Produces clean, reliable base-loaded energy and steam
- Uses less land per megawatt than other renewable energy sources
- Sustainable and steady renewable fuel source (compared to wind and solar)
- Destroys chemical waste / conventional HAPs
- Results in low emission levels, typically well below permitted levels
- Catalytically destroys NOx, dioxins and furans using an SCR
High efficiency and low emissions
Waste to energy is one of the most robust and effective alternative energy options to reduce CO2 emissions and replace fossil fuels. Approximately 2/3 of household waste is categorized as biomass. Therefore, we can recover 2/3 as CO2-neutral energy and reduce our dependence on fossil fuels.
In Europe, 50 million tons of waste is converted into valuable energy through WtE technology, supplying 27 million Europeans with electricity. Still, 50% of municipal solid waste becomes landfill. This releases greenhouse gasses like methane. Our WtE technology eliminates these emissions.
Our goals are two-fold: to maximise production and efficiency to meet energy needs, and to reduce our environmental footprint.
Do you know these Waste facts ?
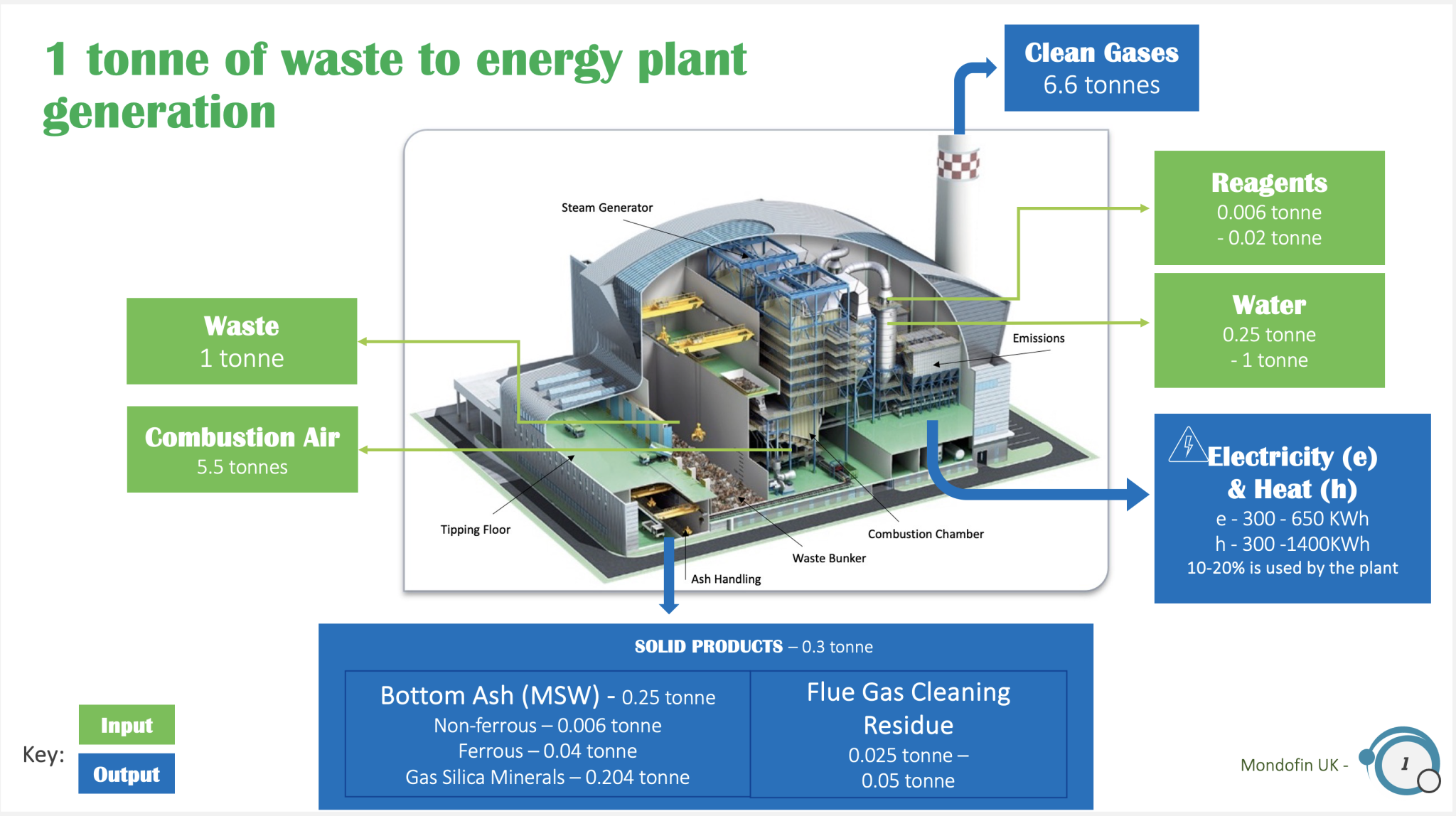
Energy from Waste Generation – 1 tonne
Energy from Waste Plant Costing
This advanced moving grate technology can be tailored to suit a very large range of capacity per line from 6t/h to 50 t/h i.e. 50 to 400 kt/y per line, with thermal input now potentially exceeding 120 MWth/line. Concerning the plant as a whole, its total capacity is recommended to be at least 150 kt/y for scale effects for theinvestment amortization and 300 to 500 kt/y capacity is the most sensible.
In the past, EfW plants had a minimum of 2 or 3 lines to ensure a continuous service all year round. Nowadays, the high availability which
is obtained on this reliable technology (+92%) allows building plants with only one line with an optimized maintenance program.
Below some orders of magnitude for costs in Eastern Europe or similar based on:
Fuel: typical Residual Municipal Solid Waste •
No land costs (considered as provided free of charge by the Authority), and ground conditions allowing conventional foundations
Project development and Permitting costs to be added
“Standard” architectural requirements •
Emissions requirements in line with the Industrial Emissions Directive
BOT contract whereby the contractor finances the CAPEX and is paid back with tipping fee per tonne of waste over 25+ years.
Well established bankability of the project with payment guarantees limited currency risk.
Energy sales: electricity only at 40- 50€/MWhe
This estimate provides some reference data which should remain valid in principle in different countries. The OPEX figures (and to a lesser extent the CAPEX) could however be significantly lower in low-income countries.
The gate fee covers CAPEX and OPEX expenditures minus the revenues from the energy selling and material recycling.
This table shows the significance of the “scale effect” when developing larger plants.
Plant Capacity kt / y | CAPEX in M (Euro) | OPEX Euro / t | Energy Rev Euro / t | Gate fee Euro / t |
150 | 150 | 40 – 50 | 20 – 30 | 80 – 100 |
500 | 300 | 30 – 40 | 20 – 30 | 50 – 80 |
Rather than the annual mass capacity, the “size” of an EfW plant for its design and its CAPEX amount are mainly fixed by the thermal power input of the plant, which is the product of its hourly capacity by the calorific value of the fuel.
For example, a facility designed to treat 10t/h of residual MSW with an LCV of 8MJ/kg will develop a thermal power of 8x10x1000/3600 = 22MWth.
It will cost and produce the same energy quantity as a facility designed to treat 8t/h of residual MSW with an LCV of 10MJ/kg with the same thermal power input of c.22MW.
This means that:
• The pre-treatment in order to increase the LCV up-stream the EfW is in general not viable (except for very low LCV to improve the self- combustion of the fuel)
• With an increase of the LCV for example from 8 to 10MJ/kg (+25%), the size of a facility with an hourly capacity of 10t/h will increase from c.22MWth to 28MWth (+25%), the CAPEX
will roughly cost 15% more, the OPEX will be roughly the same and the energy revenues will increase by 25%.