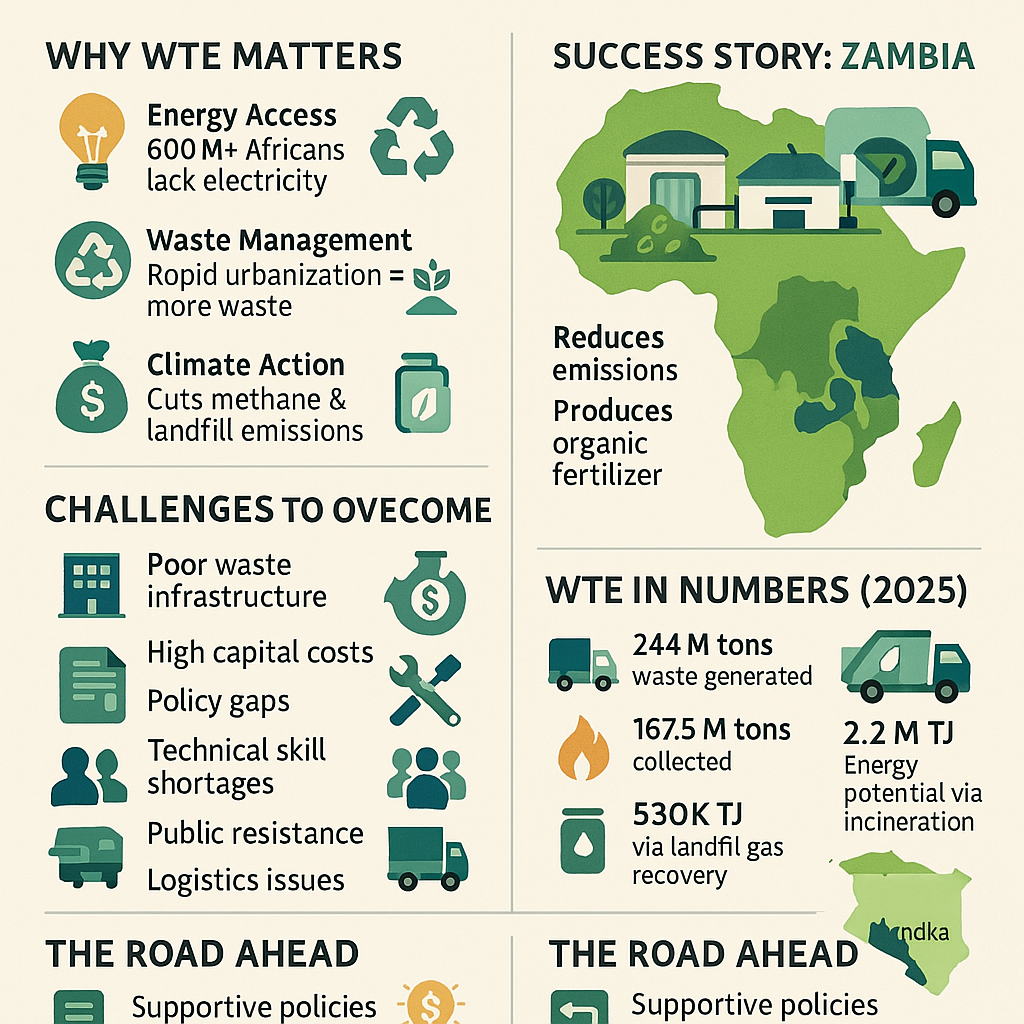
Waste-to-Energy in Africa !
🌍 Powering Progress: Waste-to-Energy in Africa’s Sustainable Future
As Africa faces the twin challenges of energy insecurity and mounting waste, a transformative solution is gaining momentum: Waste-to-Energy (WTE). By converting organic and municipal waste into clean, reliable power, WTE is helping African nations move toward a circular economy, climate resilience, and energy independence.
⚡ A New Energy Frontier
In Zambia, the Luapula Water Supply and Sanitation Company (LpWSC) is leading the way. With support from German utilities and the EU’s Water Operators’ Partnerships programme, LpWSC has built a biogas facility that captures methane from sewage and transforms it into electricity. This powers the city’s wastewater treatment plant, reduces emissions, and produces organic fertilizer for local farmers.
“This project isn’t just about energy—it’s about leadership in the face of crisis,” says Golden Manyanga, Senior Manager of Engineering at LpWSC. “By turning waste into power, we’re showing that a Zambian utility can lead the transition to clean, reliable, and homegrown energy solutions.”
🌱 Scaling Solutions Across the Continent
Zambia’s success is part of a broader movement. From Kenya to Nigeria, WTE projects are gaining traction as governments seek to diversify their energy mix and reduce dependence on fossil fuels. These initiatives are not only addressing chronic power shortages but also creating jobs, improving sanitation, and mitigating climate change.
International organizations are stepping in to accelerate this momentum. A recent partnership between the UNFCCC and the Global Energy Interconnection Development and Cooperation Organization (GEIDCO) launched the Energy Cluster, a platform aimed at strengthening clean energy capacity in developing countries. The initiative emphasizes South-South cooperation, technical training, and strategic engagement to help countries scale up WTE and other renewable energy solutions.
Despite this new frontier, there is still a very limited number of WTE facility in Africa.
Existing Projects from 2025:
Reppie Plant (Ethiopia): Africa’s first major WTE facility.
Gorge Farm (Kenya): 2.4 MW anaerobic digestion plant using vegetable and flower waste.
Bronkhorstspruit (South Africa): Industrial-scale biogas plant processing 240,000 tons of organic waste.
Ghana Hybrid Plant: 400 kW facility combining solar, biogas, and pyrolysis.
Bulawayo (Zimbabwe): Planned thermal WTE plant converting solid waste into biodiesel and electricity.
🚧 Barriers to Waste-to-Energy in Africa
Despite its promise, WTE implementation in Africa faces several challenges:
1. 🏗️ Inadequate Waste Management Infrastructure
Most cities lack efficient systems for waste collection and segregation. With over 90% of waste openly dumped or burned, reliable waste streams for WTE are hard to secure.
2. 💰 High Capital Costs and Limited Financing
WTE technologies require significant upfront investment. Limited access to financing and uncertain returns deter private investors and municipalities.
3. 📜 Policy and Regulatory Gaps
Many countries lack clear policies or incentives for WTE. The absence of feed-in tariffs and renewable energy frameworks creates uncertainty for developers.
4. 🔧 Technical and Operational Challenges
Local waste compositions often require customized technology. Additionally, there’s a shortage of skilled personnel to operate and maintain WTE facilities.
5. 🧠 Public Perception and Community Resistance
Concerns about pollution and health risks can lead to community opposition. Public awareness and engagement are crucial for project success.
6. 🚚 Logistics and Supply Chain Complexity
Fragmented waste collection systems and transportation challenges make it difficult to ensure a steady supply of waste to centralized WTE plants.
🌟 The Road Ahead
To unlock the full potential of WTE in Africa, several enablers are essential:
- Supportive policies and regulatory frameworks
- Investment in infrastructure and technology
- Public-private partnerships
- Community engagement and education
Mondofin can play a pivotal role by developing a turnkey project, facilitating financing, sharing technical expertise, EPC, and advocating for sustainable energy policies.
Africa’s waste is no longer just a problem—it’s a powerful resource. With the right vision and collaboration, WTE can light up communities, clean up cities, and power a greener, more resilient future.
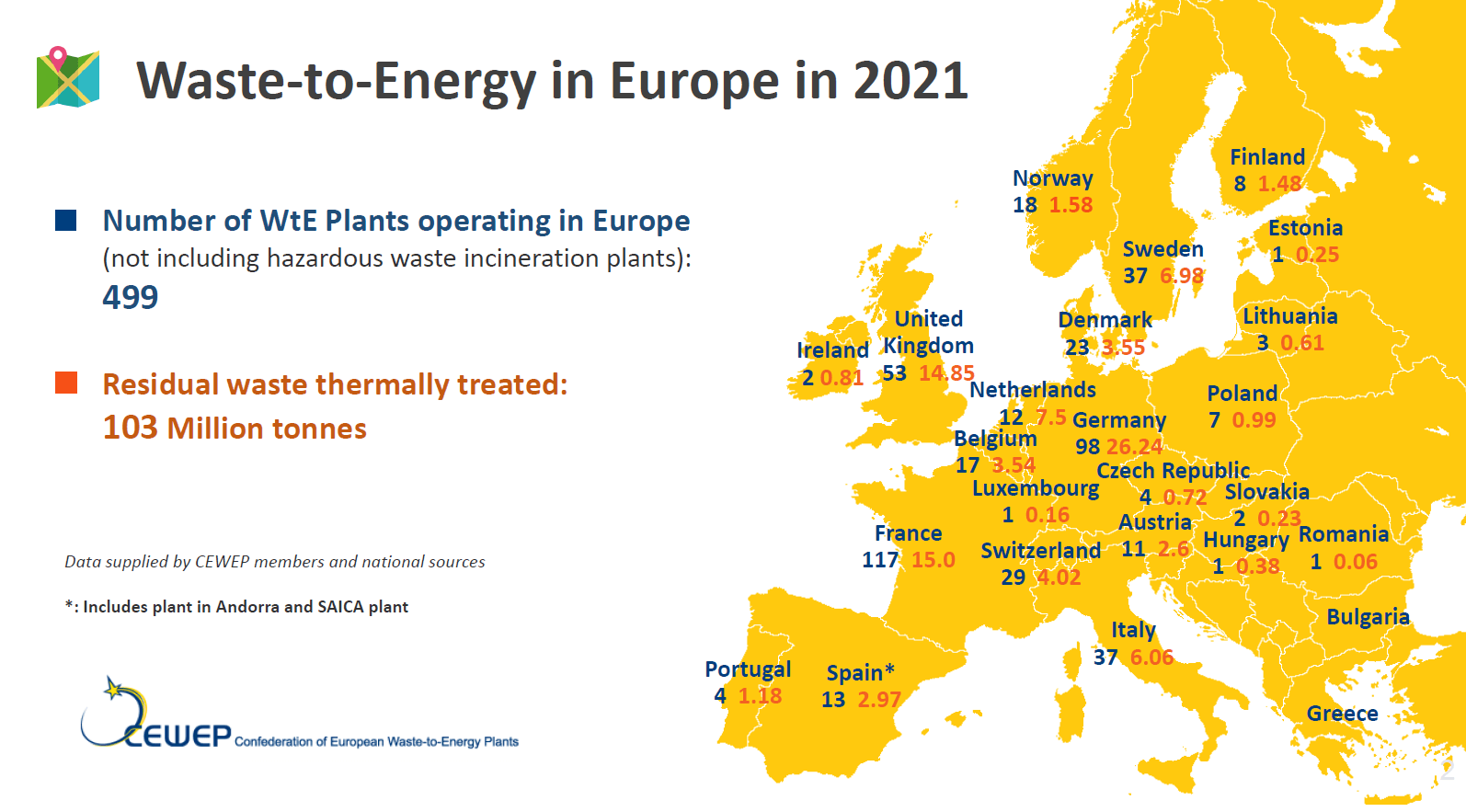
Why we opt for Incineration Technology ?
The Reality
Nowadays, the global market presents numerous technologies for recovering energy from waste, so why do we opt for incineration? Alternative technologies such as pyrolysis, gasification, or plasma treatment are also widely recognized.
In our everyday activities, we face various prevalent misconceptions regarding incineration. These misconceptions result in a complete misunderstanding of the prominence and functions of contemporary waste-to-energy technologies. That is the reason we believe it is necessary to provide commentary on the existing technology.
The map below illustrates the number of waste-to-energy plants in Europe alone (blue numbers) along with the amount of waste in million tons being incinerated annually (red numbers).
Waste to Energy Plants in Europe
Each year, CEWEP publishes a map of Waste-to-Energy plants in Europe, based on data coming from CEWEP members and national sources.
This overview shows that Waste-to-Energy treatment capacity was overall stable compared to 2020, with a small increase in capacity.
THe overall number of facilities slightly decreased compared to 2020 due to a change in our data collection methodology.
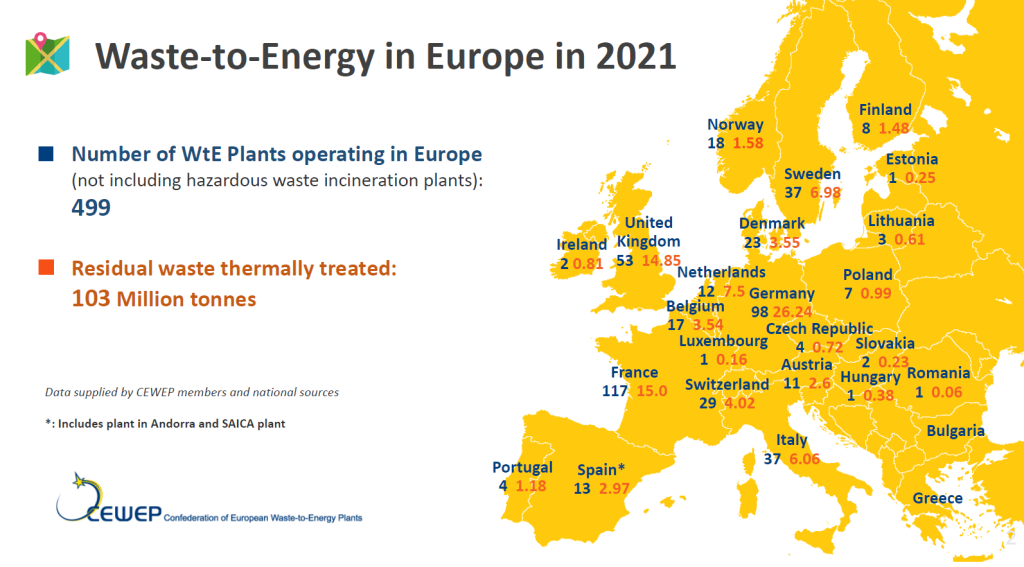
CEWEP EU Map for WTE 2021
The Hard Truth
Even if we do not provide incineration plants to our clients, we must reference incineration as a benchmark. Because it is a globally dominant, well-recognized technology. Incineration is not being dismissed, as some commentators have indicated, but rather the opposite. An extract from the extensive 1000-page plus report “Waste to Energy 2024/2025” by Ecoprog, a reputable consultant known for thorough market analysis, can be downloaded. ecoprog extract link 2024/2025
Ecoprog states: “As of early 2024, there were more than 2,800 WtE plants worldwide, reaching a disposal capacity of about 576 million tons per year. We estimate about 3,100 plants with a capacity of more than 700 million tons to be operational by 2033. This is 600 more increase as predicted from the 2,200 WtE facilities operational around the globe 10 years ago. ” As indicated on page 4 of the extract, ECOPROG only accounts for “9. 2 Thermal treatment: incineration and gasification” technologies. This is due to the fact that other technologies such as pyrolysis and plasma treatment hold a minimal market share.
It is challenging to pitch incineration plants to clients because frequently, public perception is influenced by speculation and misinformation about the market. Nonetheless, what is clear is that we need to evaluate any technology against incineration, as it remains the most validated and widespread technology globally. We cannot draw comparisons between our offerings and questionable pyrolysis manufacturers, whose systems lack a proven history of success.
Thus, when we present any other alternative waste to energy technology mainly aimed at MSW, we consistently compare CAPEX, OPEX, capacity factor, and energy generation with incineration plants of comparable capacity. This approach provides our client with a solid foundation for comprehending the project and technology.
And indeed, incineration continues to evolve and has not yet made its final mark in the global waste-to-energy sector.
The Industry Barometer
2024 was a favourable year for Waste-to-Energy (WtE), according to the yearly Waste-to-Energy Industry Barometer.
The report shows an increase in optimism among WtE plant operators, with the business climate index climbing to 91. 7 points in 2024 from 87. 6 in 2023; this is amidst a challenging economic landscape.
The Barometer also points to an enhancement in plant utilization, with 66% of participants indicating high usage compared to 42% last year.
The results show increasing optimism among WtE plant operators. Gate fees are expected to rise, especially in Germany, where the implementation of a CO₂ levy in January 2024 has heightened expenses for WtE facilities. At the same time, 95% of plant operators assessed their current business situation as “good” or “satisfactory,” underscoring the sector’s durability under escalating pressures.
The report also highlights considerable obstacles to progressing carbon management technologies, including high investment expenses, insufficient regulatory frameworks, and infrastructure issues such as the absence of CO₂ transport pipelines.
While 61% of operators are in discussions about carbon capture initiatives, only 14% have made significant moves towards implementation.
Numerous industry stakeholders consider carbon management crucial for meeting the EU’s net-zero emissions objectives, yet advancement is slow. Operators emphasize the critical need for financial incentives and legal clarity to promote carbon capture and help achieve the EU’s net-zero ambitions.
Globally, Europe continues to be the largest market for WtE technologies, but the emphasis has shifted towards maintaining and modernizing aging infrastructure instead of new developments.
Beyond Europe, market growth is sluggish in areas such as India and Brazil, where insufficient financial incentives, regulatory hurdles, and public perception challenges impede development. In China, a significant drop in WtE projects, influenced by the real estate crisis, has diminished its global impact, although it remains the leading WtE market by capacity.
The Industry Barometer stresses the significance of favorable policies and investments to maintain the sector’s growth. The findings support a comprehensive strategy for waste management, acknowledging the contribution of WtE in meeting environmental objectives while tackling economic and technical challenges.
Reference – https://www.cewep.eu/wp-content/uploads/2024/10/Industry-Barometer-Waste-to-Energy-2024.pdf
Read More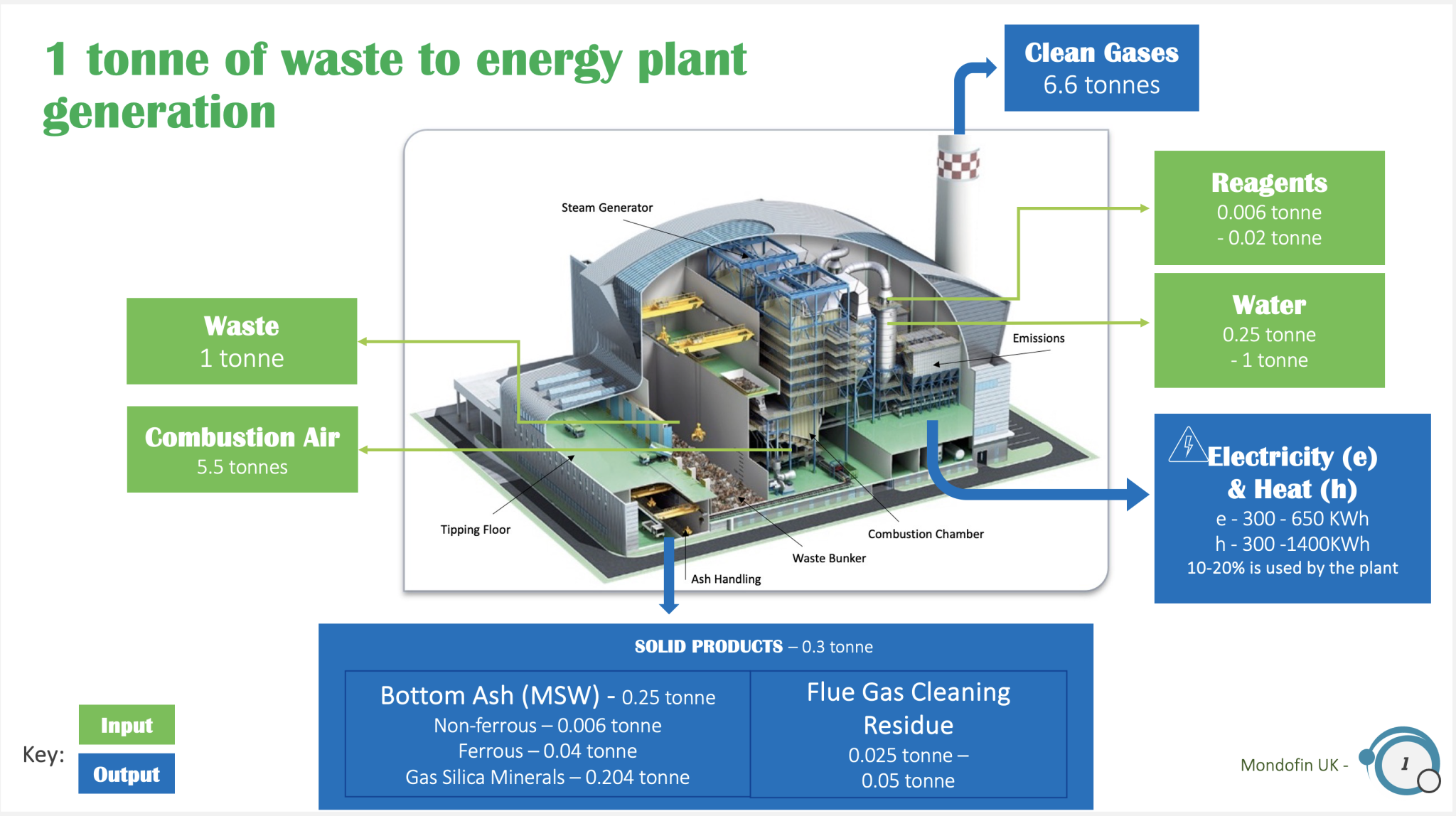
What is Waste-to-Energy (WTE)?
Ecologically Sound, Cost-Effective Energy
Waste to energy (WtE) is a vital part of a strong and sustainable waste management chain. Fully complementary to recycling, it is an economically and ecologically sound way to provide a renewable source for energy while diverting waste from landfills.
A WtE plant converts solid waste into electricity and/or heat – an ecological, cost-effective way of energy recovery.
A waste-to-energy (or energy-from-waste) plant converts municipal and industrial solid waste into electricity and/or heat for industrial processing and for district heating systems – an ecologically sound, cost-effective means of energy recovery. The energy plant works by burning waste at high temperatures and using the heat to make steam. The steam then drives a turbine that creates electricity.
Recover valuable resources
Energy from waste (EfW) isn’t just a trash disposal method. It’s a way to recover valuable resources. Today, it is possible to reuse 90% of the metals contained in the bottom ash. And the remaining clinker can be reused as road material.
The results and benefits are proven:
- Avoids methane emissions from landfills
- Offsets greenhouse gas (GHG) emissions from fossil fuel electrical production
- Recovers/recycles valuable resources, such as metals
- Produces clean, reliable base-loaded energy and steam
- Uses less land per megawatt than other renewable energy sources
- Sustainable and steady renewable fuel source (compared to wind and solar)
- Destroys chemical waste / conventional HAPs
- Results in low emission levels, typically well below permitted levels
- Catalytically destroys NOx, dioxins and furans using an SCR
High efficiency and low emissions
Waste to energy is one of the most robust and effective alternative energy options to reduce CO2 emissions and replace fossil fuels. Approximately 2/3 of household waste is categorized as biomass. Therefore, we can recover 2/3 as CO2-neutral energy and reduce our dependence on fossil fuels.
In Europe, 50 million tons of waste is converted into valuable energy through WtE technology, supplying 27 million Europeans with electricity. Still, 50% of municipal solid waste becomes landfill. This releases greenhouse gasses like methane. Our WtE technology eliminates these emissions.
Our goals are two-fold: to maximise production and efficiency to meet energy needs, and to reduce our environmental footprint.
Do you know these Waste facts ?
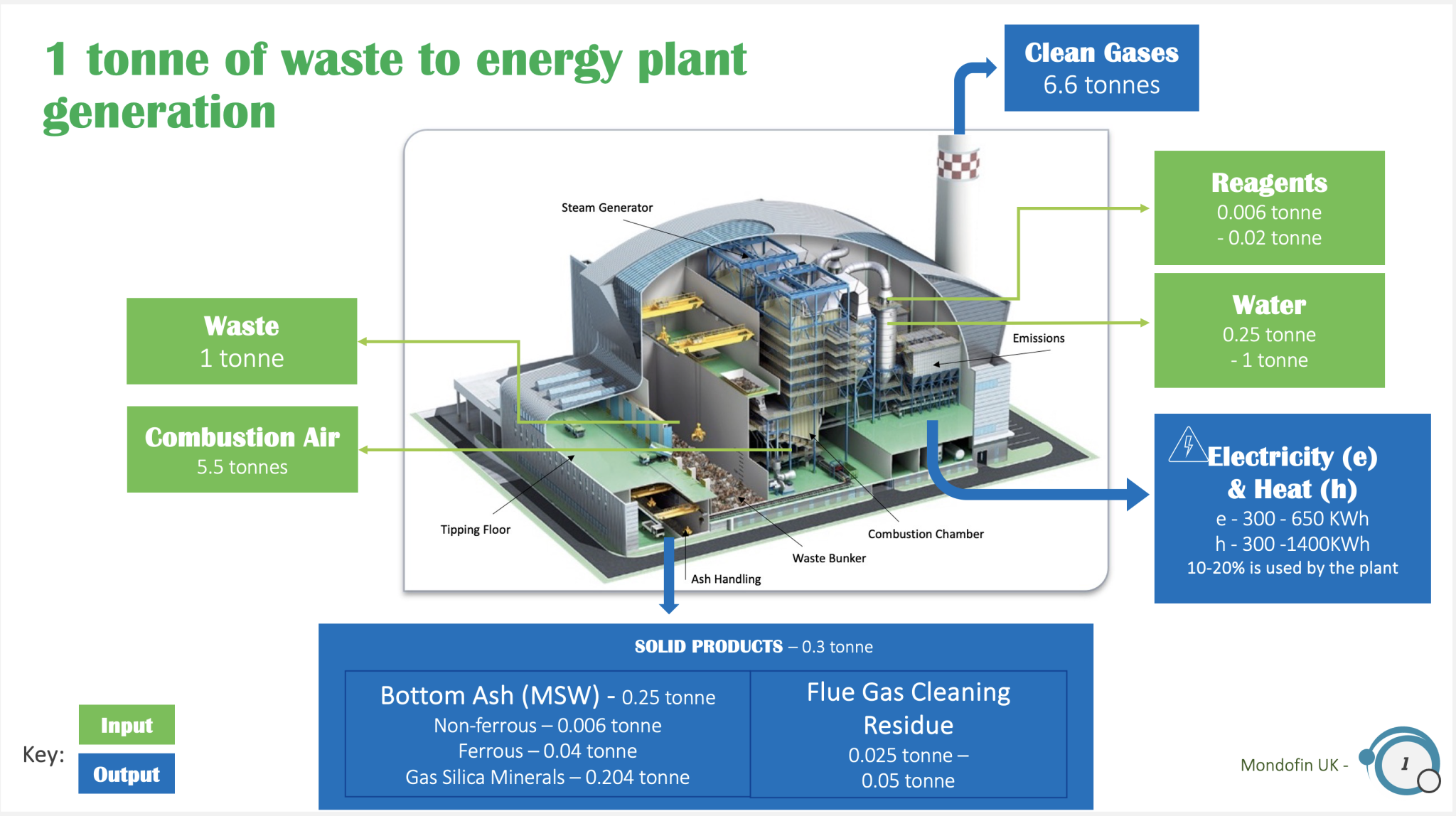
Energy from Waste Generation – 1 tonne
Energy from Waste Plant Costing
This advanced moving grate technology can be tailored to suit a very large range of capacity per line from 6t/h to 50 t/h i.e. 50 to 400 kt/y per line, with thermal input now potentially exceeding 120 MWth/line. Concerning the plant as a whole, its total capacity is recommended to be at least 150 kt/y for scale effects for theinvestment amortization and 300 to 500 kt/y capacity is the most sensible.
In the past, EfW plants had a minimum of 2 or 3 lines to ensure a continuous service all year round. Nowadays, the high availability which
is obtained on this reliable technology (+92%) allows building plants with only one line with an optimized maintenance program.
Below some orders of magnitude for costs in Eastern Europe or similar based on:
Fuel: typical Residual Municipal Solid Waste •
No land costs (considered as provided free of charge by the Authority), and ground conditions allowing conventional foundations
Project development and Permitting costs to be added
“Standard” architectural requirements •
Emissions requirements in line with the Industrial Emissions Directive
BOT contract whereby the contractor finances the CAPEX and is paid back with tipping fee per tonne of waste over 25+ years.
Well established bankability of the project with payment guarantees limited currency risk.
Energy sales: electricity only at 40- 50€/MWhe
This estimate provides some reference data which should remain valid in principle in different countries. The OPEX figures (and to a lesser extent the CAPEX) could however be significantly lower in low-income countries.
The gate fee covers CAPEX and OPEX expenditures minus the revenues from the energy selling and material recycling.
This table shows the significance of the “scale effect” when developing larger plants.
Plant Capacity kt / y | CAPEX in M (Euro) | OPEX Euro / t | Energy Rev Euro / t | Gate fee Euro / t |
150 | 150 | 40 – 50 | 20 – 30 | 80 – 100 |
500 | 300 | 30 – 40 | 20 – 30 | 50 – 80 |
Rather than the annual mass capacity, the “size” of an EfW plant for its design and its CAPEX amount are mainly fixed by the thermal power input of the plant, which is the product of its hourly capacity by the calorific value of the fuel.
For example, a facility designed to treat 10t/h of residual MSW with an LCV of 8MJ/kg will develop a thermal power of 8x10x1000/3600 = 22MWth.
It will cost and produce the same energy quantity as a facility designed to treat 8t/h of residual MSW with an LCV of 10MJ/kg with the same thermal power input of c.22MW.
This means that:
• The pre-treatment in order to increase the LCV up-stream the EfW is in general not viable (except for very low LCV to improve the self- combustion of the fuel)
• With an increase of the LCV for example from 8 to 10MJ/kg (+25%), the size of a facility with an hourly capacity of 10t/h will increase from c.22MWth to 28MWth (+25%), the CAPEX
will roughly cost 15% more, the OPEX will be roughly the same and the energy revenues will increase by 25%.
Mondofin UK receives letter of intent from the Sindh Government to develop a 50MW Waste-to-Energy project in Karachi, Pakistan


Mondofin UK, through its local partner BRV, received on April 1 a signed letter of intent (LOI) to develop a Waste-to-Energy project with a capacity of up to 50 megawatts. The project expects to process 1,500 tonnes of waste per day with an estimated investment of $150 million US dollars. Mondofin UK will execute the project with Babcock and Wilcox and licensee CSET.
The Sindh Government entered into an agreement with Mondofin UK through its local partner BRV Renewable Energy (BRV) and Technology partner Babcock and Wilcox (B&W) for launching a Waste-to-Energy project to transform the residual municipal solid waste generated in Karachi into clean electricity. At the same ceremony, the Sindh Government issued LOI’s to three other consortia.
For these four projects, the Sindh Government will provide land near the landfill site in Karachi. Energy Minister Mr. Imtiaz Shaikh said “Investments of approximately 600 million US dollars is expected for these projects and of the 15,000 tonnes of waste that Karachi’s population generates on a daily basis, about 6,000 to 8,000 tonnes of waste will be processed by the WtE plants for the production of 150 megawatts of energy”. He also mentioned that this project, launched in accordance with the “Green Energy, Clean Karachi” initiative, will not only help process the garbage from Karachi in a sustainable way but will also help meet Pakistan’s renewable energy requirements.
Energy Minister Mr. Imtiaz Shaikh, Karachi administrator Mr. Barrister Murtaza Wahab, Managing Director of Sindh Solid Waste Management Board, Mr. Zuhair Channa, Consuls General of the United States and the United Arab Emirates, the Ambassador of The Netherlands, Mr. Wouter Plomp and representatives of Mondofin UK, Babcock and Wilcox, and BRV Renewable Energy attended the signing ceremony.
Karachi Project Next steps after LOI
The LOI issued by the Sindh Government sets a clear pathway of milestones towards financial close which will take approximately 18 months. It is clear that after the successful construction of many wind projects with a cumulative installed capacity of more than 1GW, Pakistan is ready to make next steps, by implementing WtE to further reduce its carbon footprint and secure reliable as well as sustainable baseload power.
To develop the facility, Mondofin UK will work with its partner Babcock and Wilcox (B&W) via its licensee Beijing China Sciences Runyu Environmental Protection Technology (CSET) to deploy the same expertise used to build the CIXI Zhongke facility, which is one of the most efficient and cleanest and automated in the world. The plant in China commissioned in 2007, can generate around 920kWh of electricity from each tonne of waste processes 2250 tonnes daily. In 2016, The Ministry of Housing and Urban-Rural Development In 2016, rated CIXI Zhongke facility as an “AA-level domestic waste incineration plant” by. Mondofin UK expects similar success from its Pakistan project.


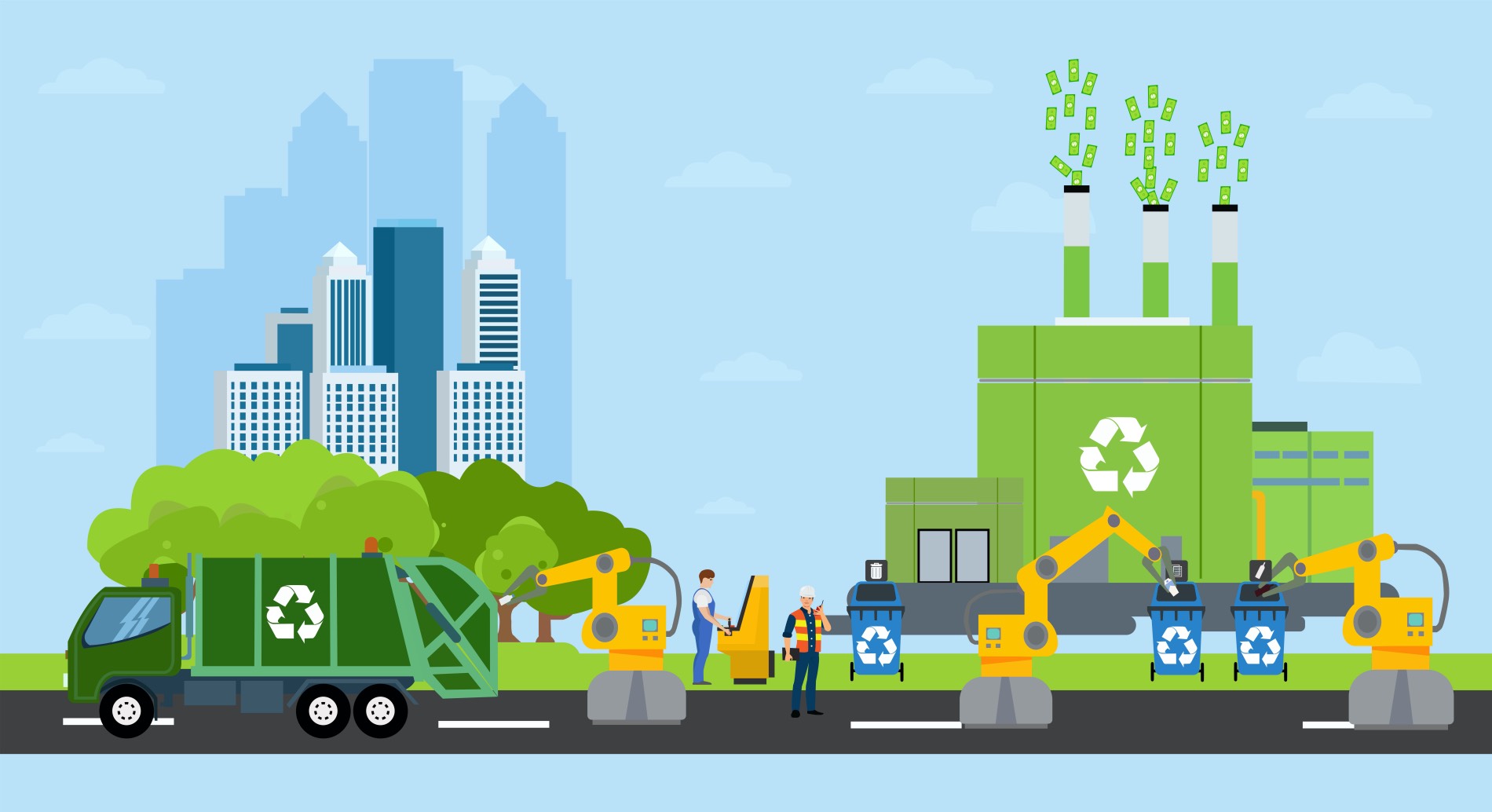
Refuse Derived Fuel
What exactly is RDF? Is it a secondary product or a waste? And is it available on the open market as a cheap renewable fuel?
RDF is refuse-derived fuel and it is produced as an output from materials recycling facilities (MRFs). It is composed of treated residual waste that is not suitable for recycling.
Although the residual waste has been through a treatment process, the manufacture of RDF does not qualify as recovery and the RDF is still classified as waste. Unlike secondary fuels based on waste solvents, it does not have such a high calorific value as fossil fuels and cannot be used as a direct replacement for them. Instead, it is burned in energy from waste (EfW) plants. RDF is regulated in the same way as any other waste and can only be burned in an installation that complies with the requirements for waste incinerators, taken from the EU Industrial Emissions Directive.
Energy from waste can be classified as either disposal by incineration or recovery (code R1), based on whether its primary purpose is to produce energy or dispose of waste. The Waste Framework Directive distinguishes between disposal and recovery using a formula based on the efficiency of the plant. Defra explains this as follows.
The R1 formula calculates the energy efficiency of the municipal solid waste incinerator and expresses it as a factor. This is based on the total energy produced by the plant as a proportion of the energy of the fuel (both traditional fuels and waste) that is incinerated in the plant. It can only be considered recovery if the value of this factor is above a certain threshold. It is important to note that the calculated value arrived at via the R1 formula is not the same as power plant efficiency, which is typically expressed as a percentage.